My task was to create the gearbox that would house the gears, spool, motor, encoder, and temperature probe while being mounted to the aluminum extrusion frame we were using for testing.
Above is a video demonstrating the finished ratcheting mechanism in action.
first draft gearbox cad (above)
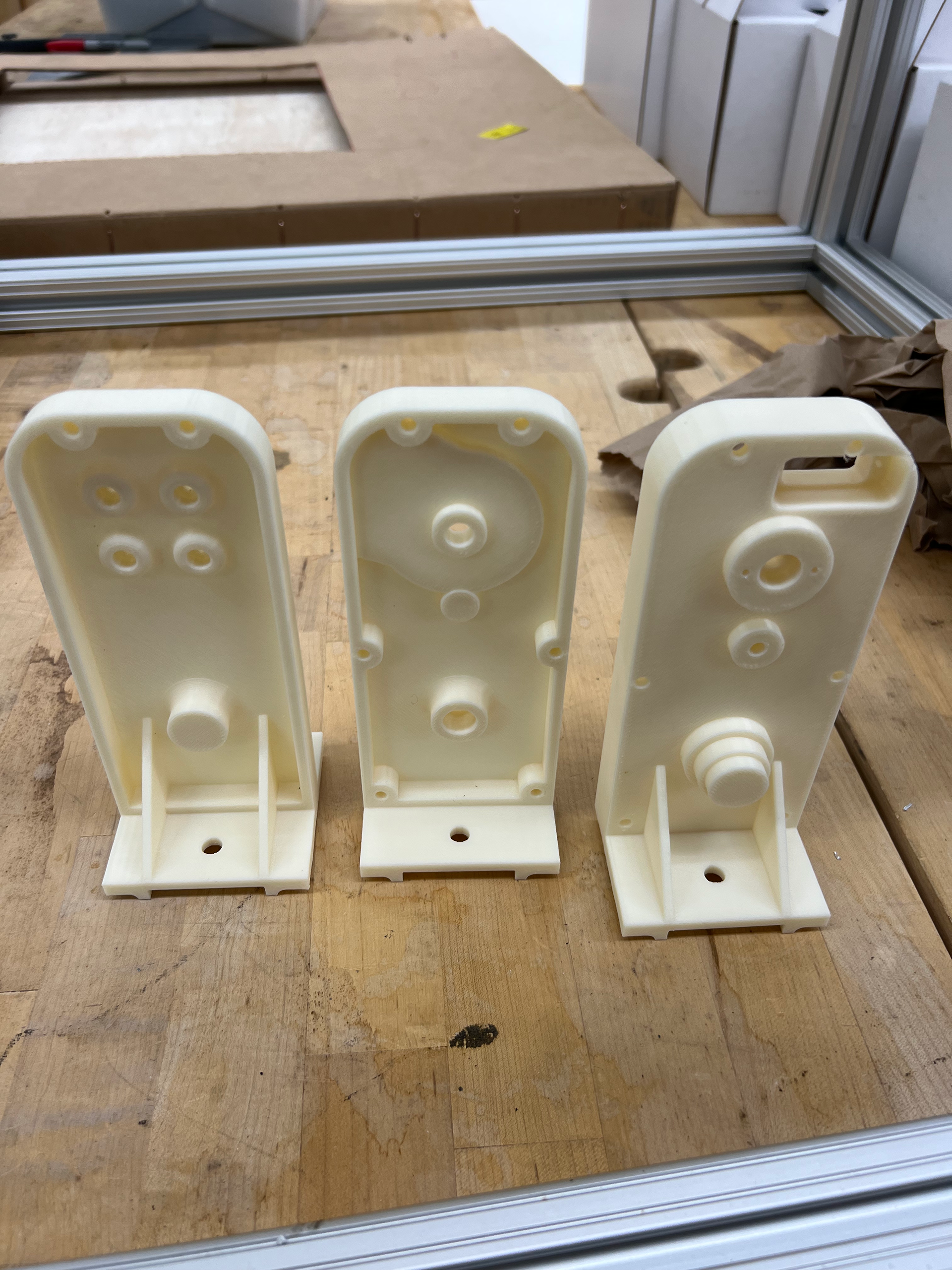
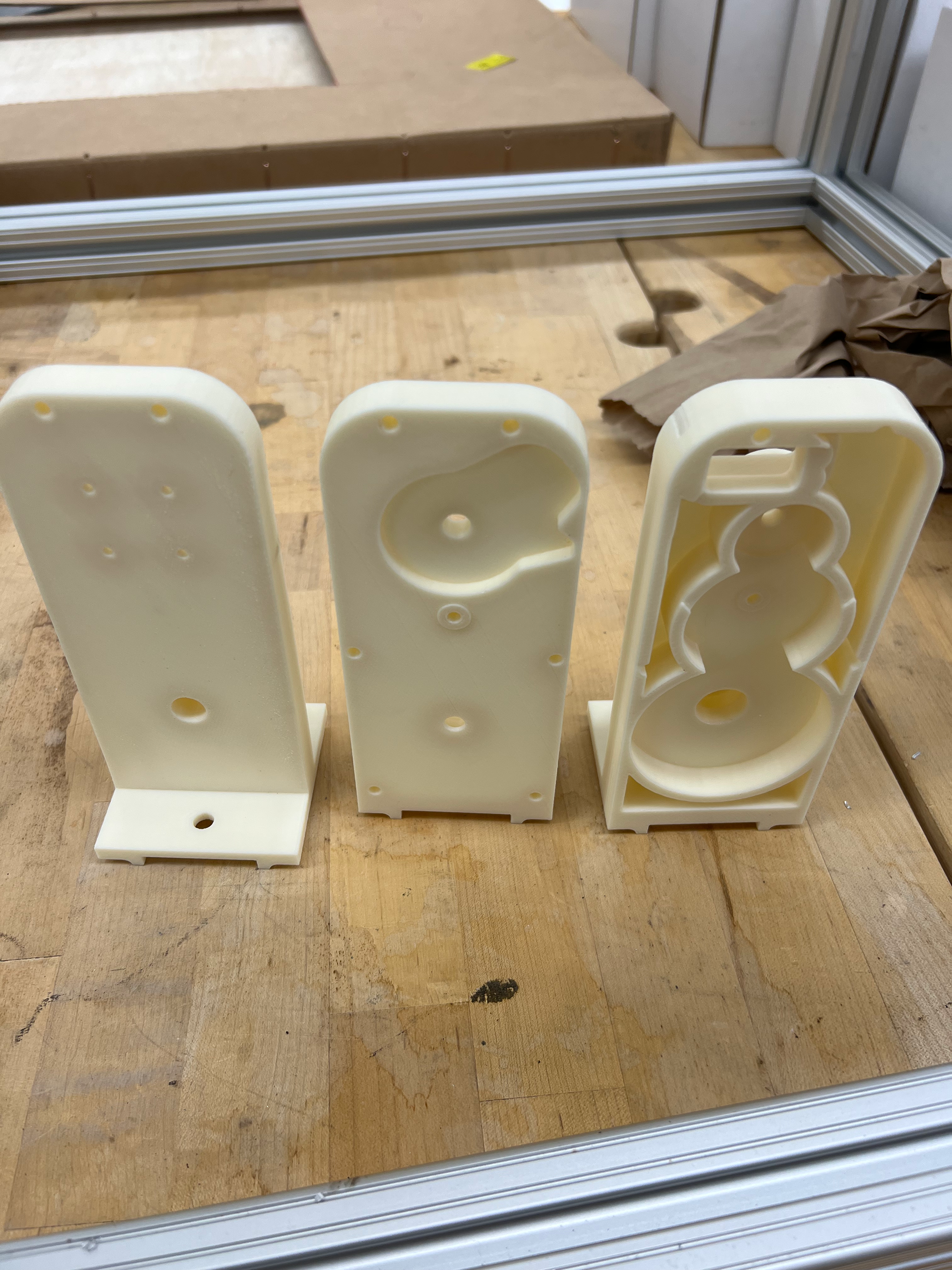
first printed parts! these were sent out to be printed by a third part on a large format fdm machine (stratasys).(above)
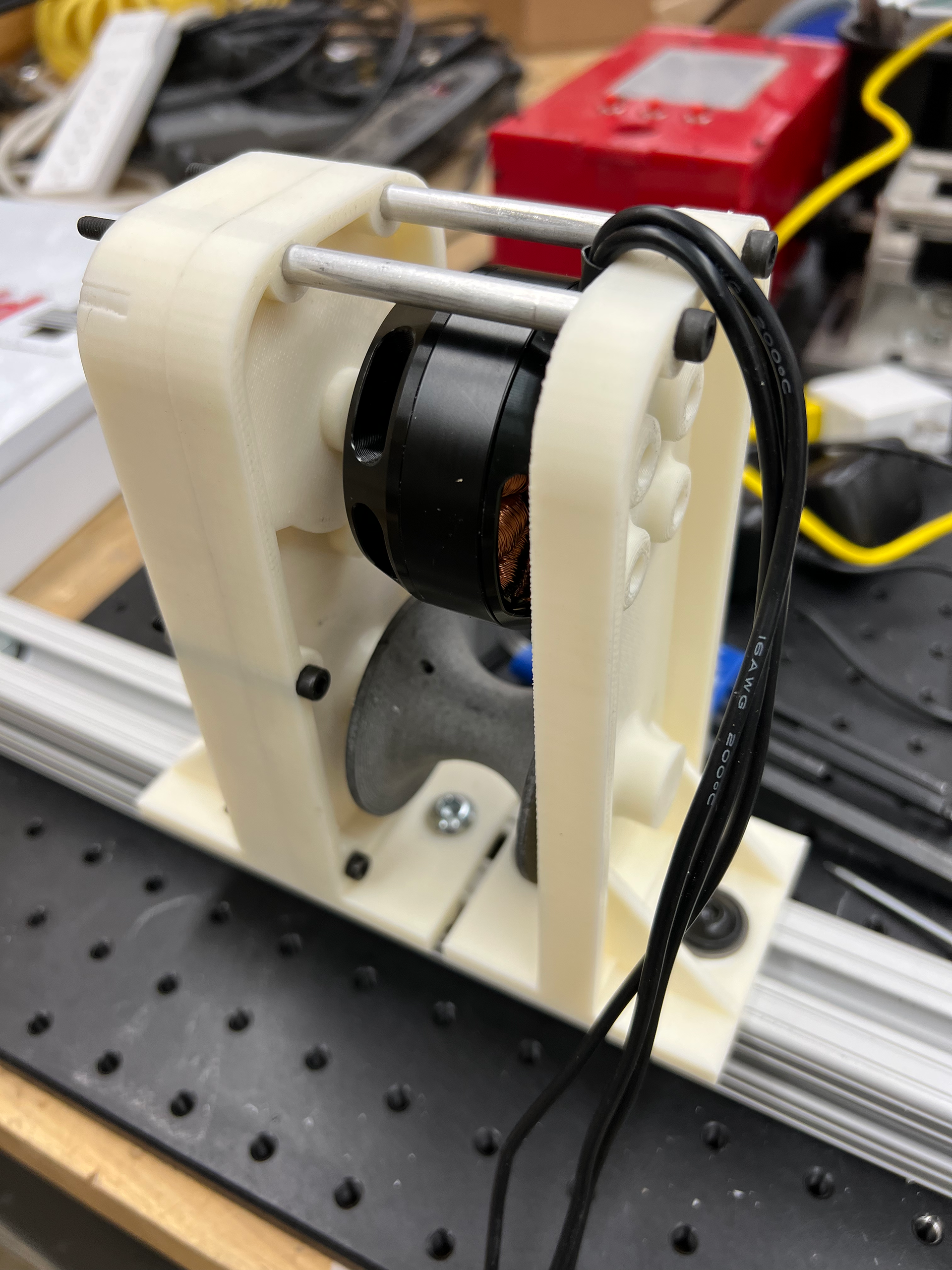
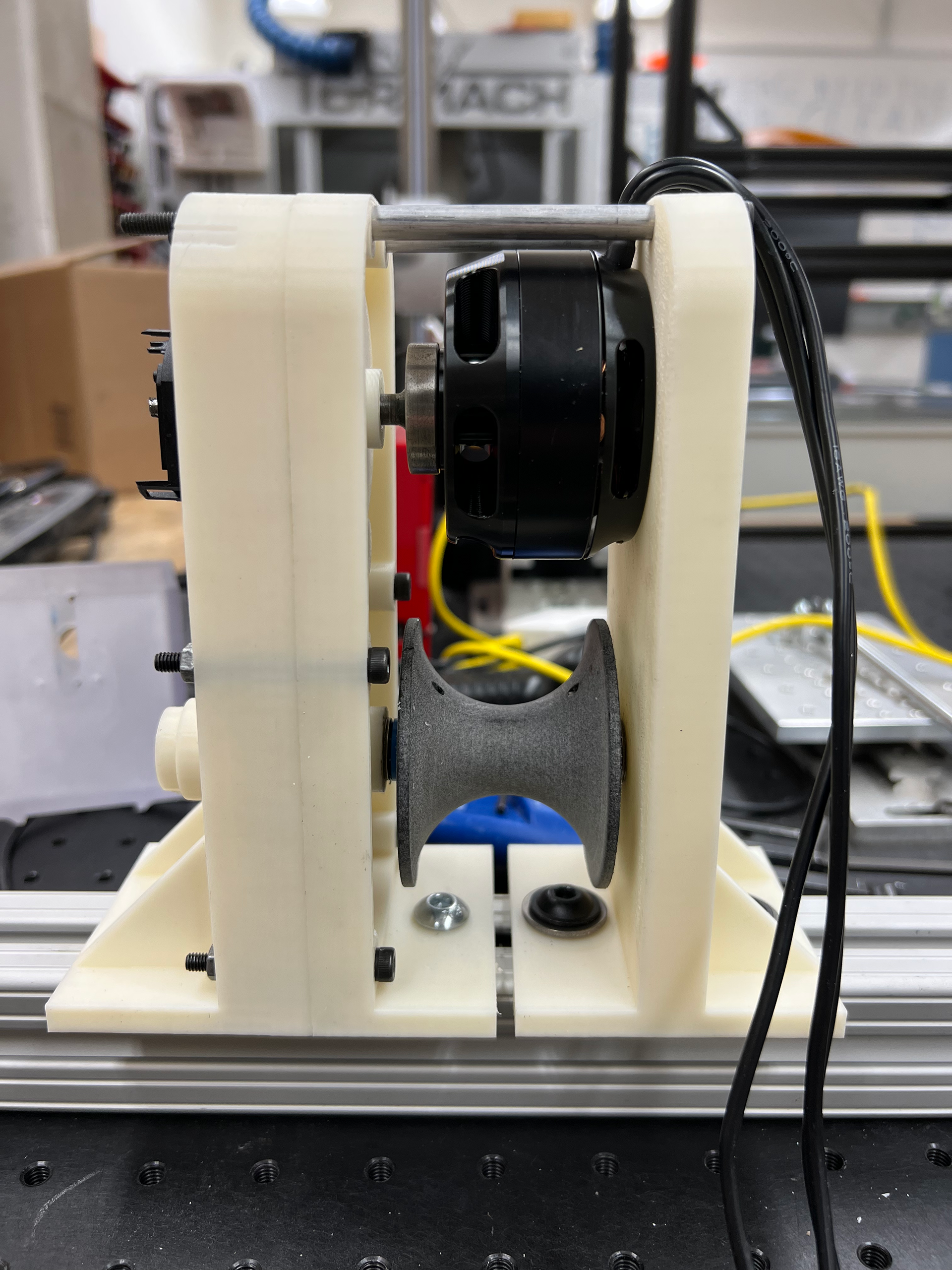

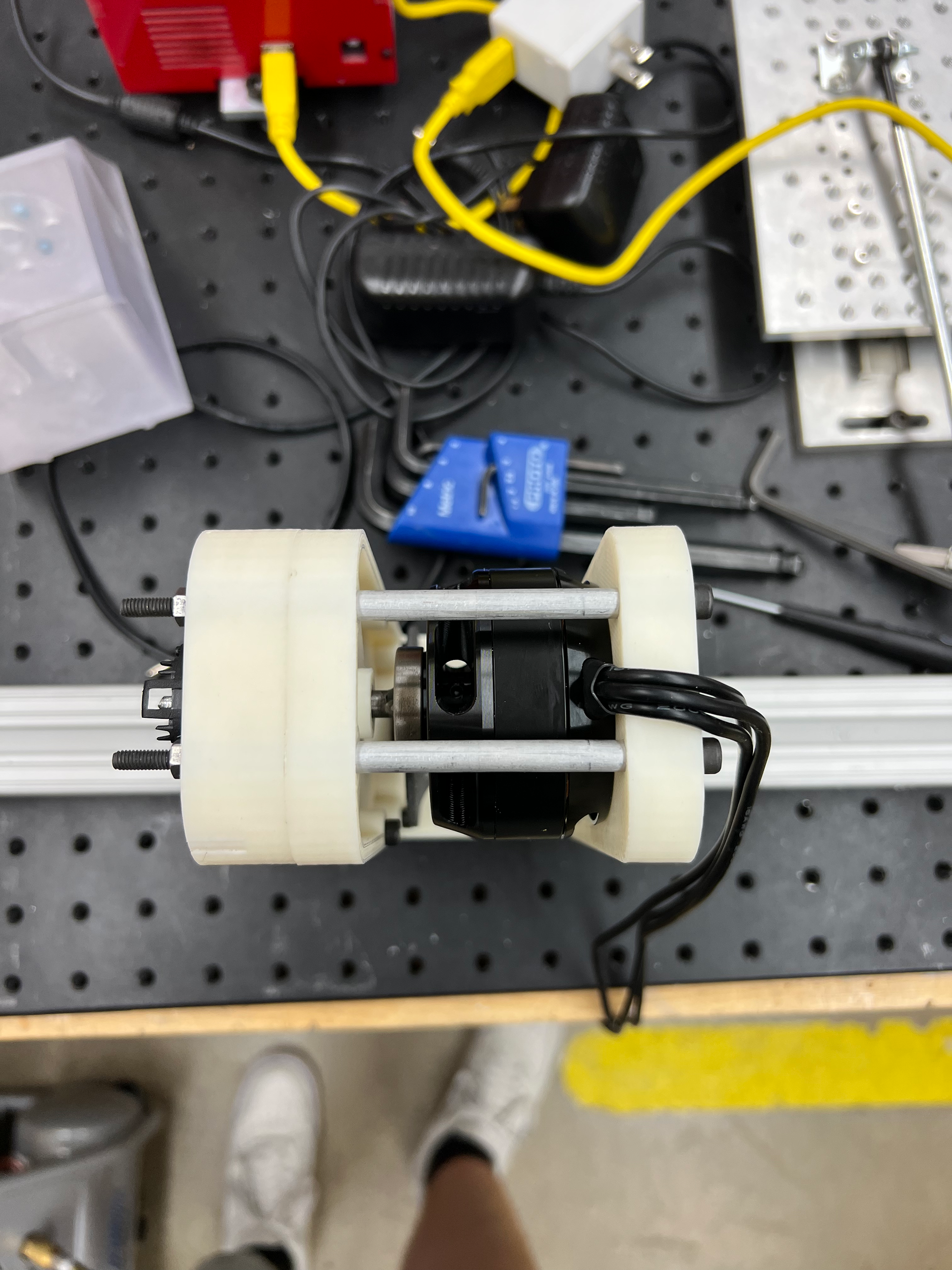
First full completed assembly mounted onto aluminum extrusion.
This assembly melted when the motor got significantly hotter than the electrical engineers expected. (above)
(bldc's are tricky)
motor shaft was not concentric, as seen in the video with the drill and the dial test indicator on the lathe (below), so I designed a new part and ordered it from a third party for the next revision.
Taking advantage of the melting issue, I used the opportunity to reprint a better revision: I and added stronger supports, windows to see the gears, better mounting features, improved fit, higher temperature resistance and reduced stress concentrations while maintaining dfm and printability.
Above is the new revision of the cad for the gearbox.
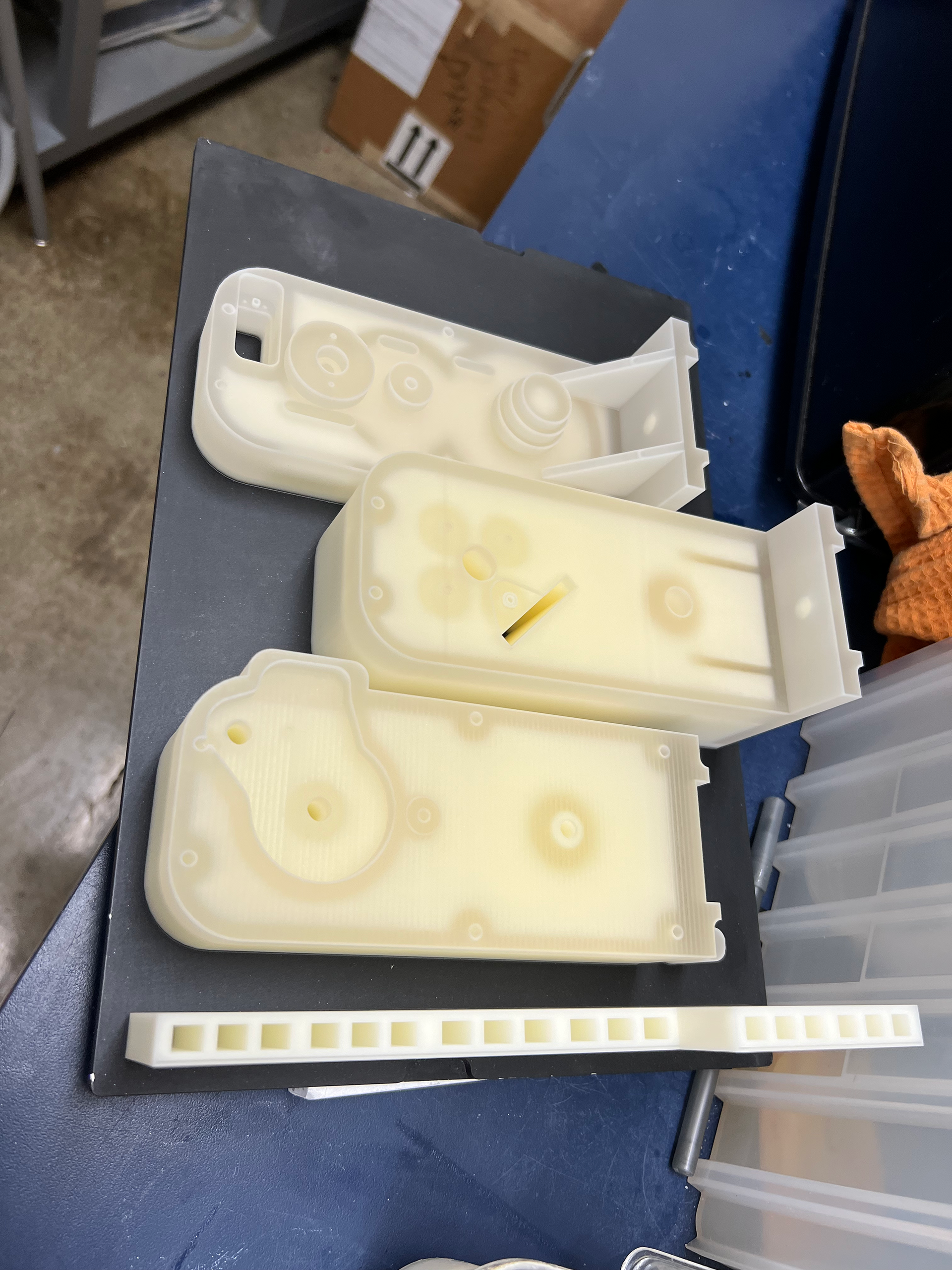
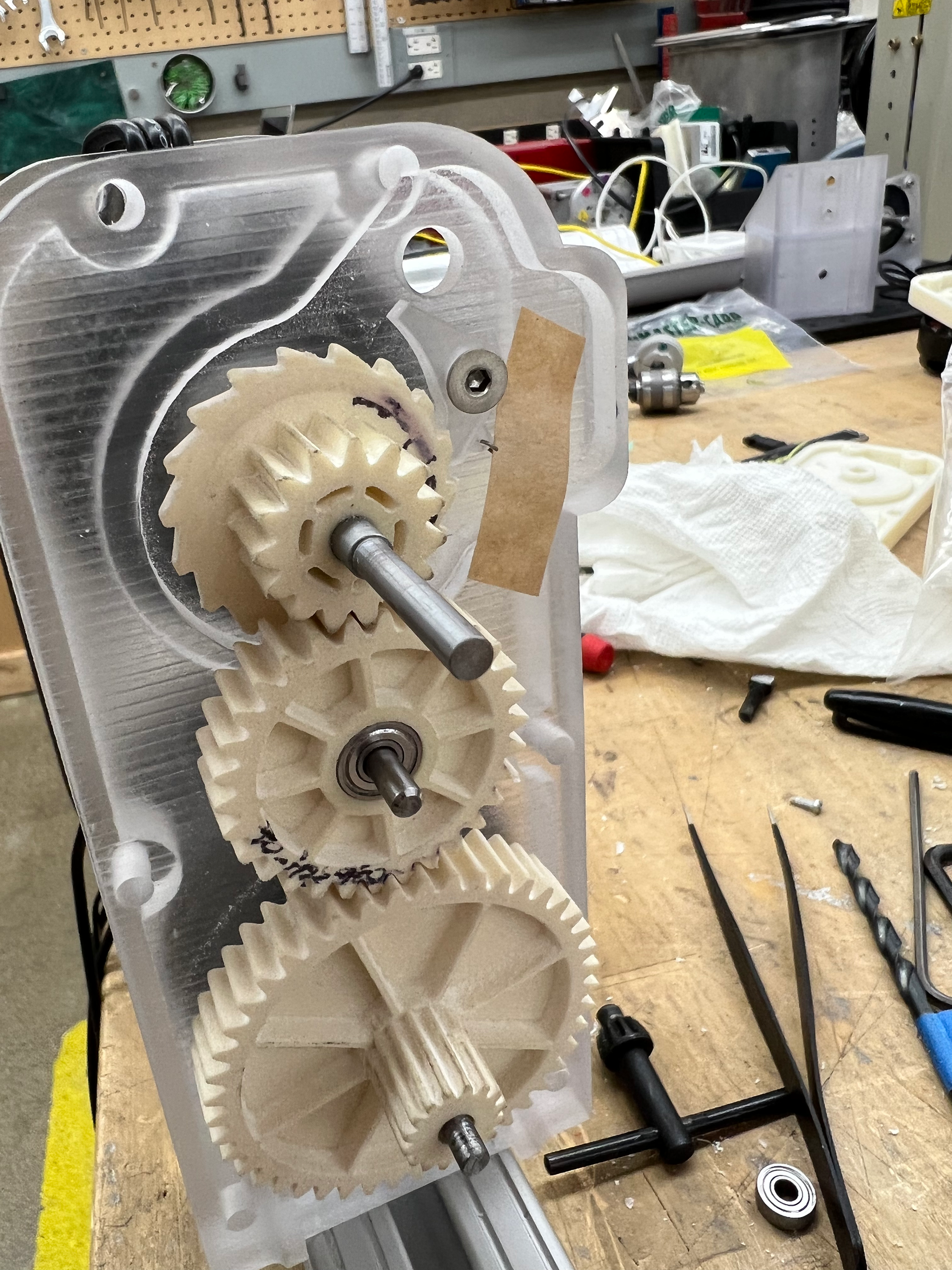
new revision's print straight off the machine prior to post-processing and finished part with hardware installed (above).
these parts allowed for many additional weeks of testing prior to production parts to arrive, helping us to meet the client deadline.