my task was to create a hand tool for operators working on the assembly line to use to install a torsion spring.
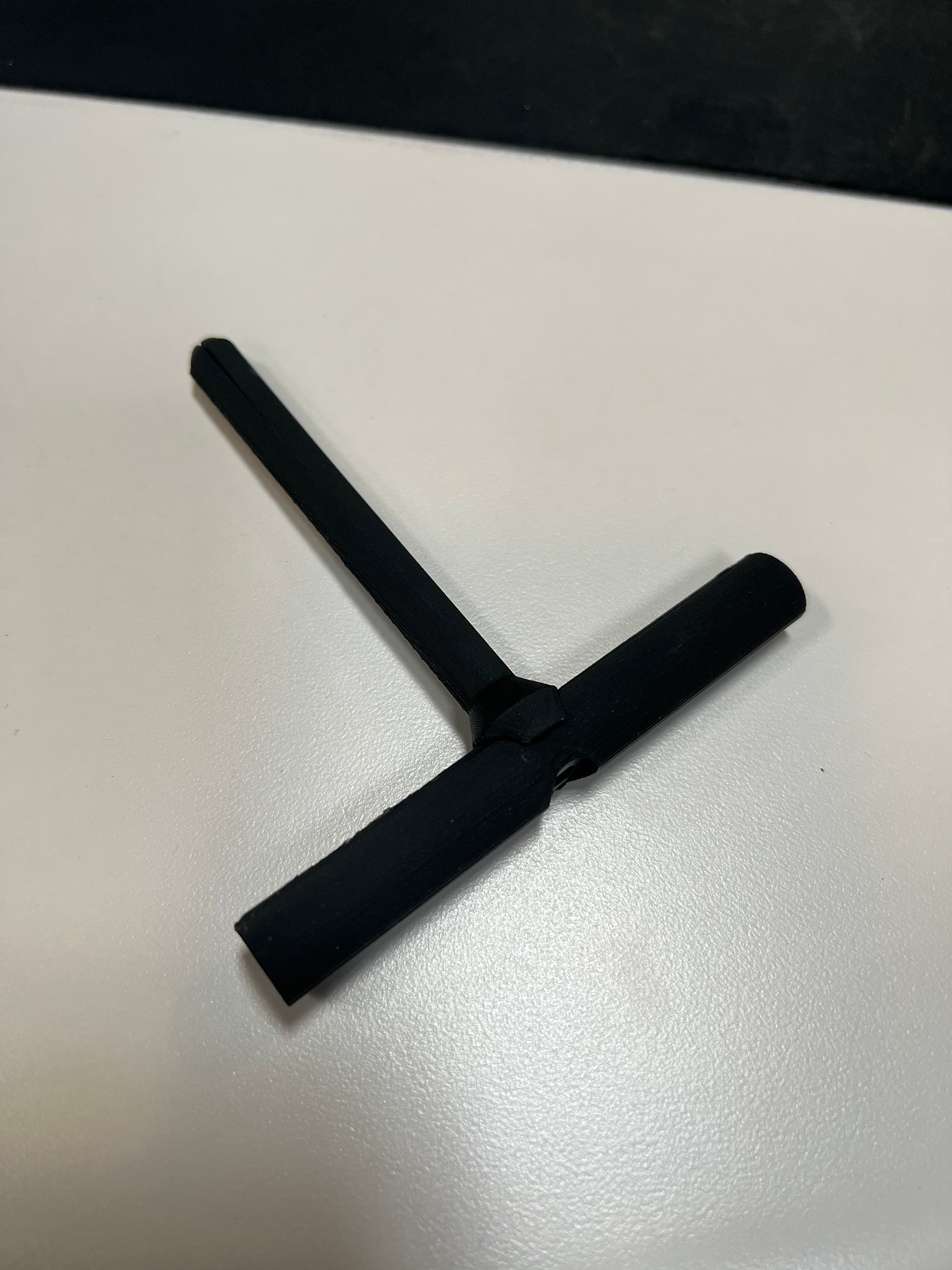
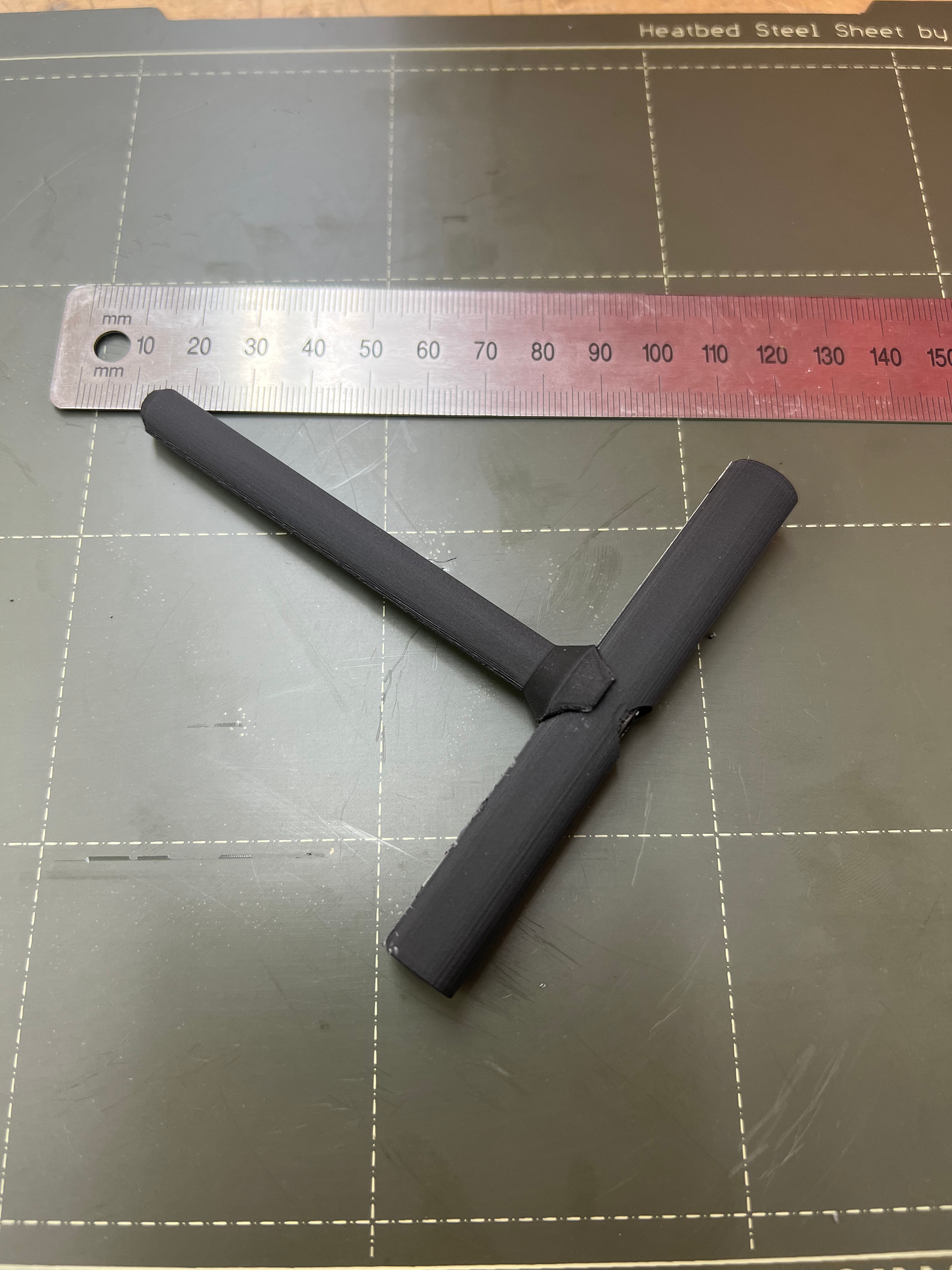
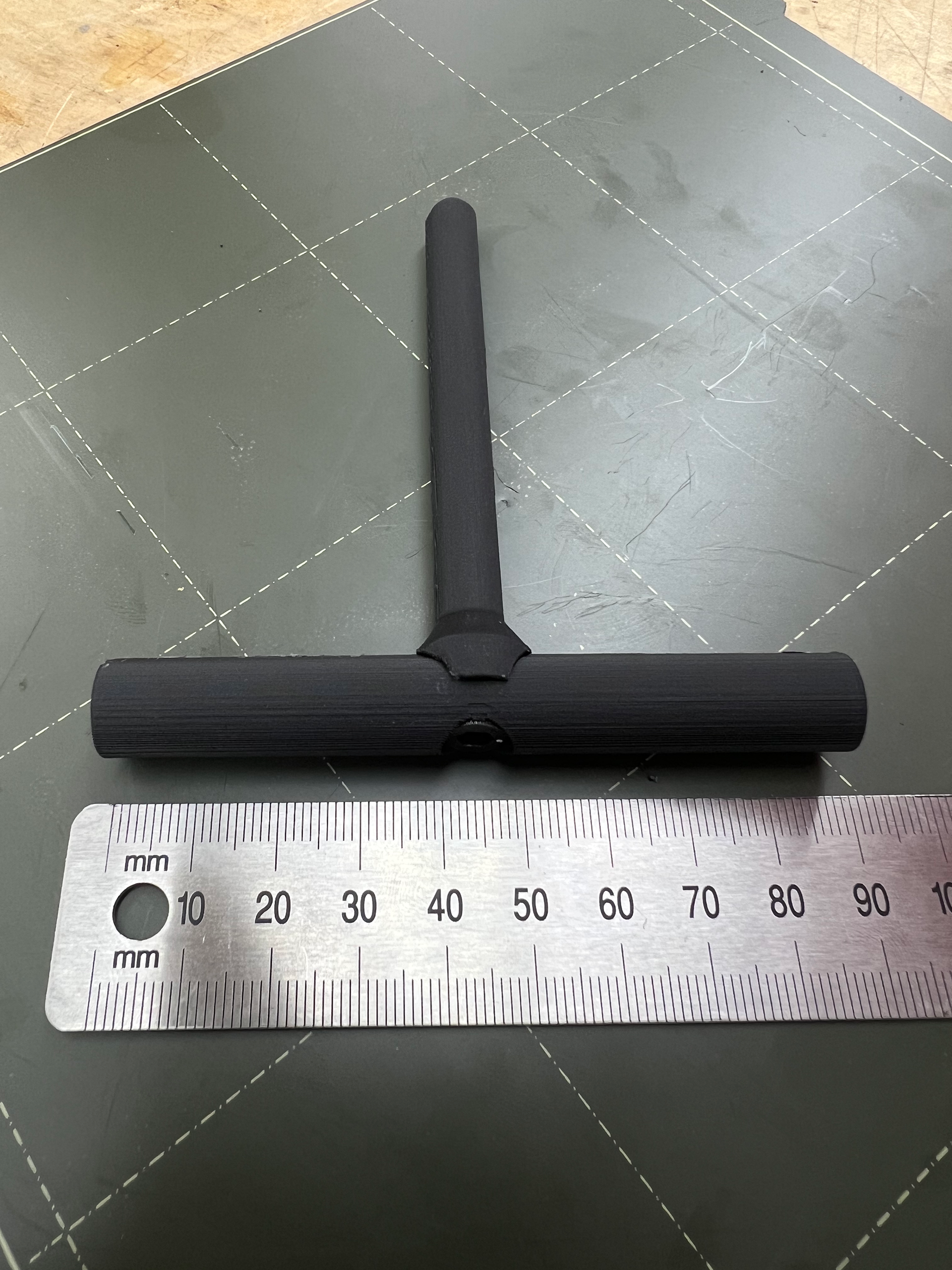
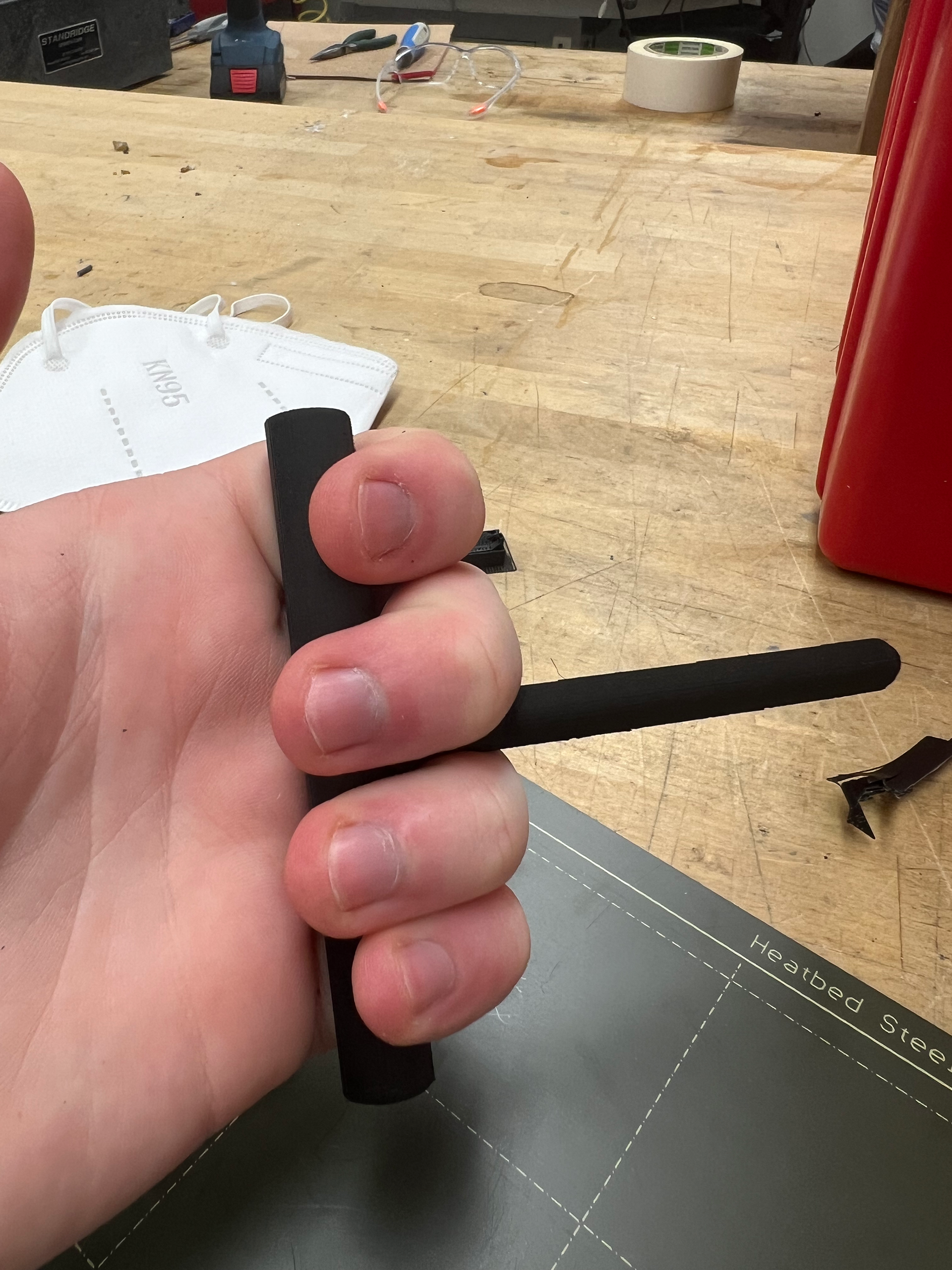
based on a quick and dirty fdm prototype in-hand, I added some length on the handle to accommodate for multiple grip types and added chamfers.
Cad of new revision is below
Cad of new revision is below
The final cad revision included careful attention to nominal dimensions and tolerances to ensure the tool functioned well, and a slightly oversized Outer diameter to ensure solid lockup. Chamfers were added for operator safety and comfort.
SHCS used for simple and sturdy fastening. Typical designs include a small set screw, which can break and get lost easily. Large standard size SHCS chosen for easier sourcing and frustration-free assembly and maintenance, as well as excellent fastening strength.
Aluminum handle and stainless steel shaft chosen to save costs while maintaining wear resistance over entire 100k+ uses in lifetime.
SHCS used for simple and sturdy fastening. Typical designs include a small set screw, which can break and get lost easily. Large standard size SHCS chosen for easier sourcing and frustration-free assembly and maintenance, as well as excellent fastening strength.
Aluminum handle and stainless steel shaft chosen to save costs while maintaining wear resistance over entire 100k+ uses in lifetime.
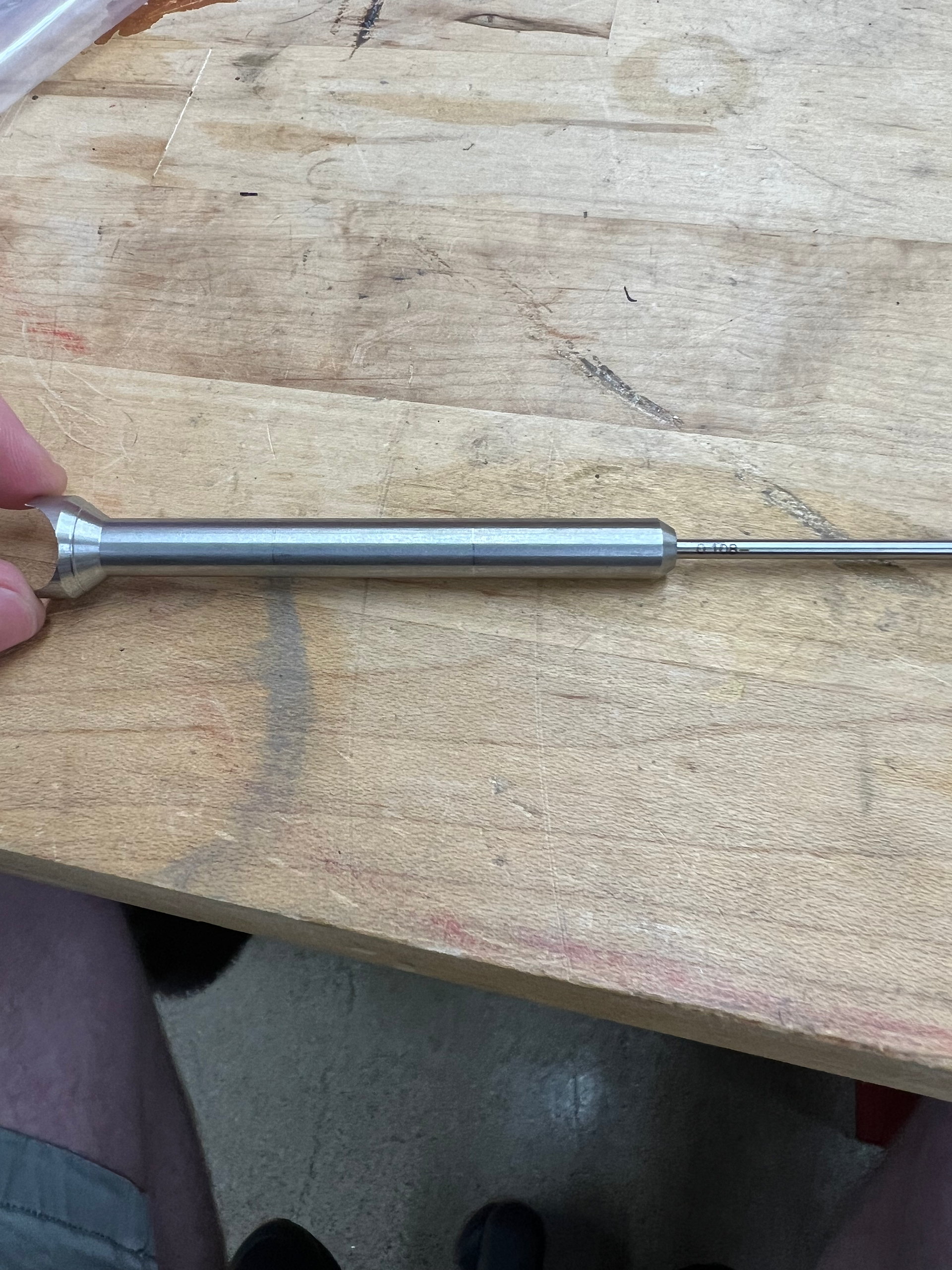
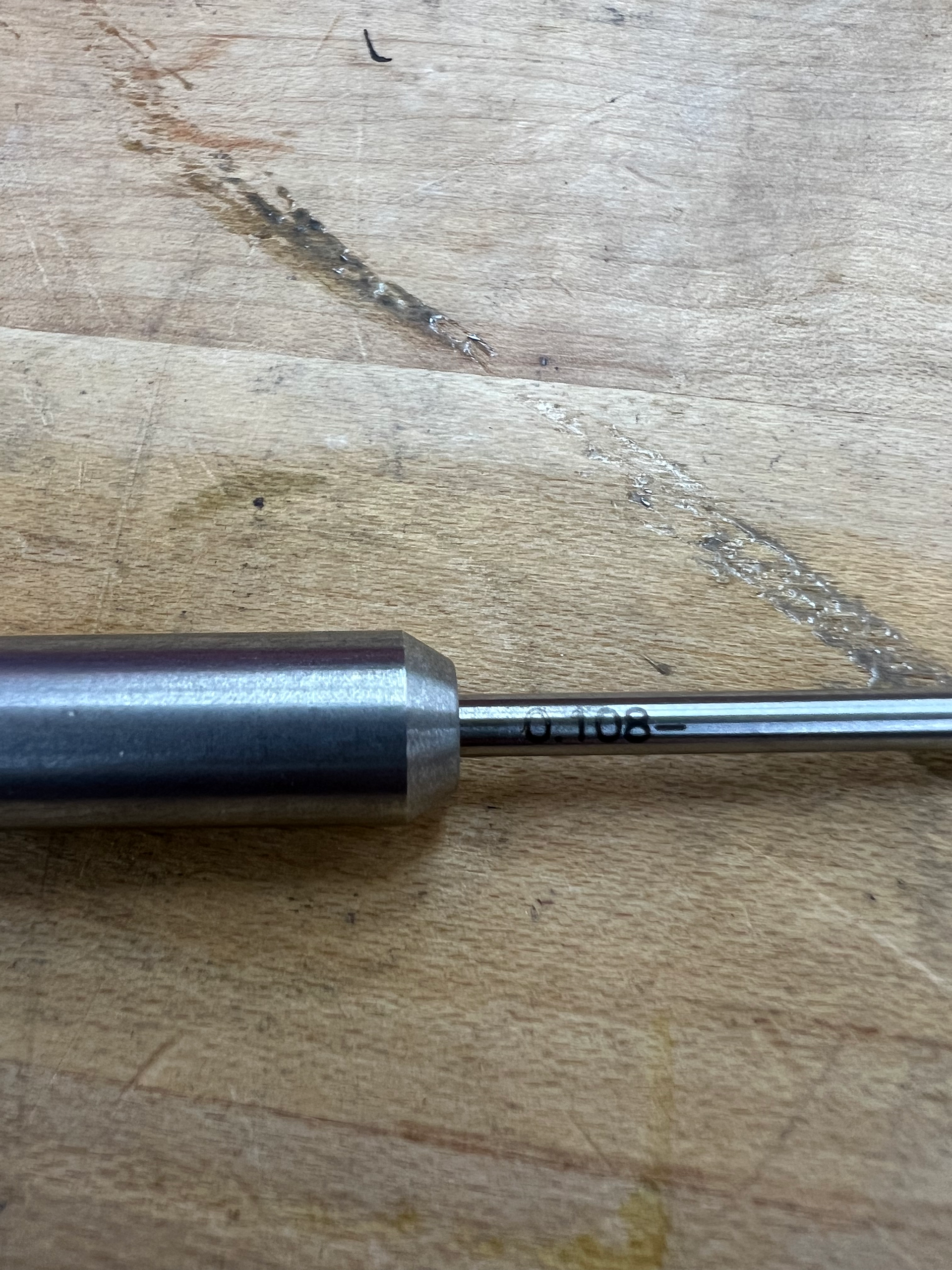
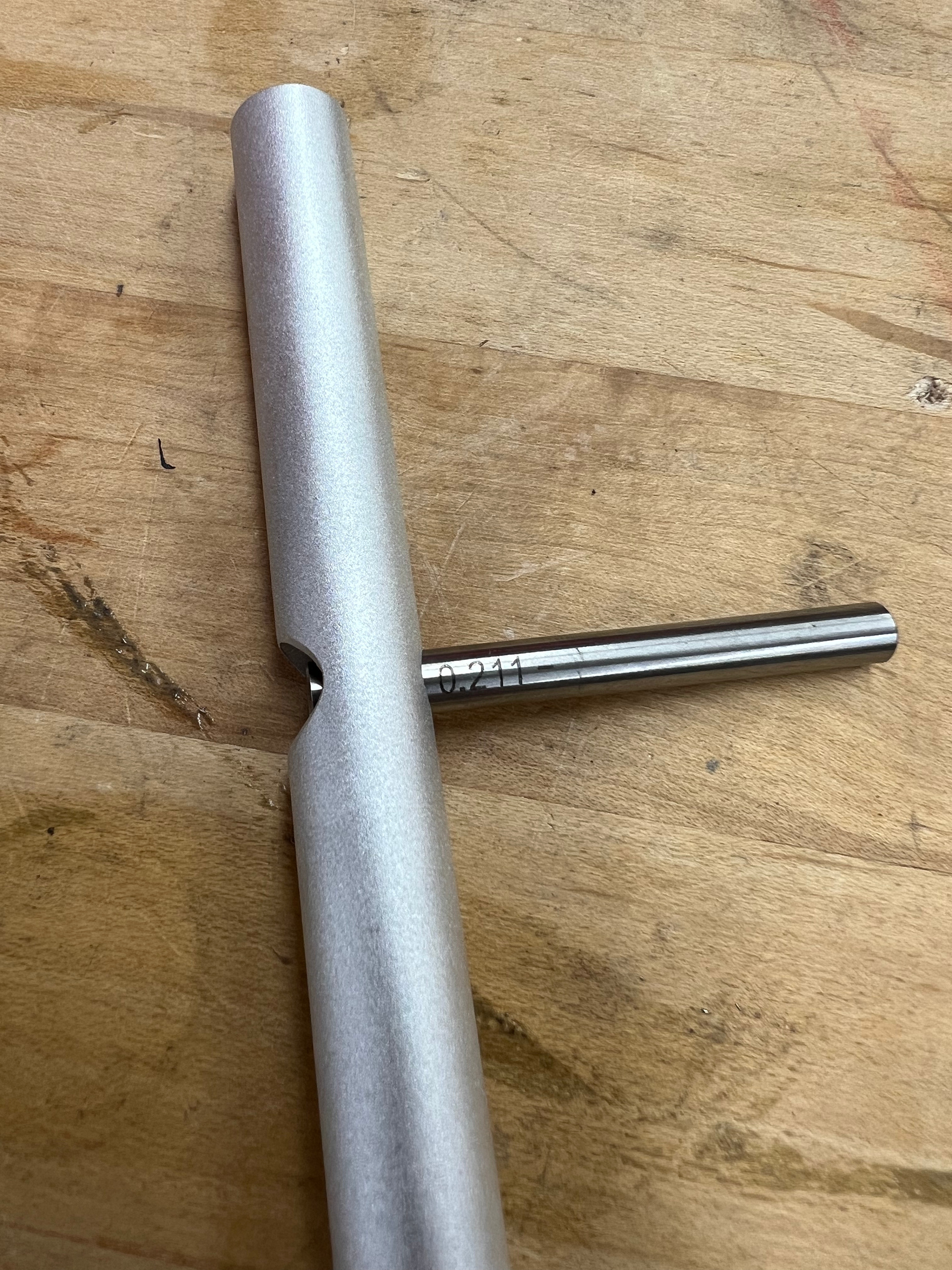
Gauge pins used to measure diameter of holes. Parts were all machined within spec, so I assembled them and sent them to the client 2 weeks ahead of schedule!
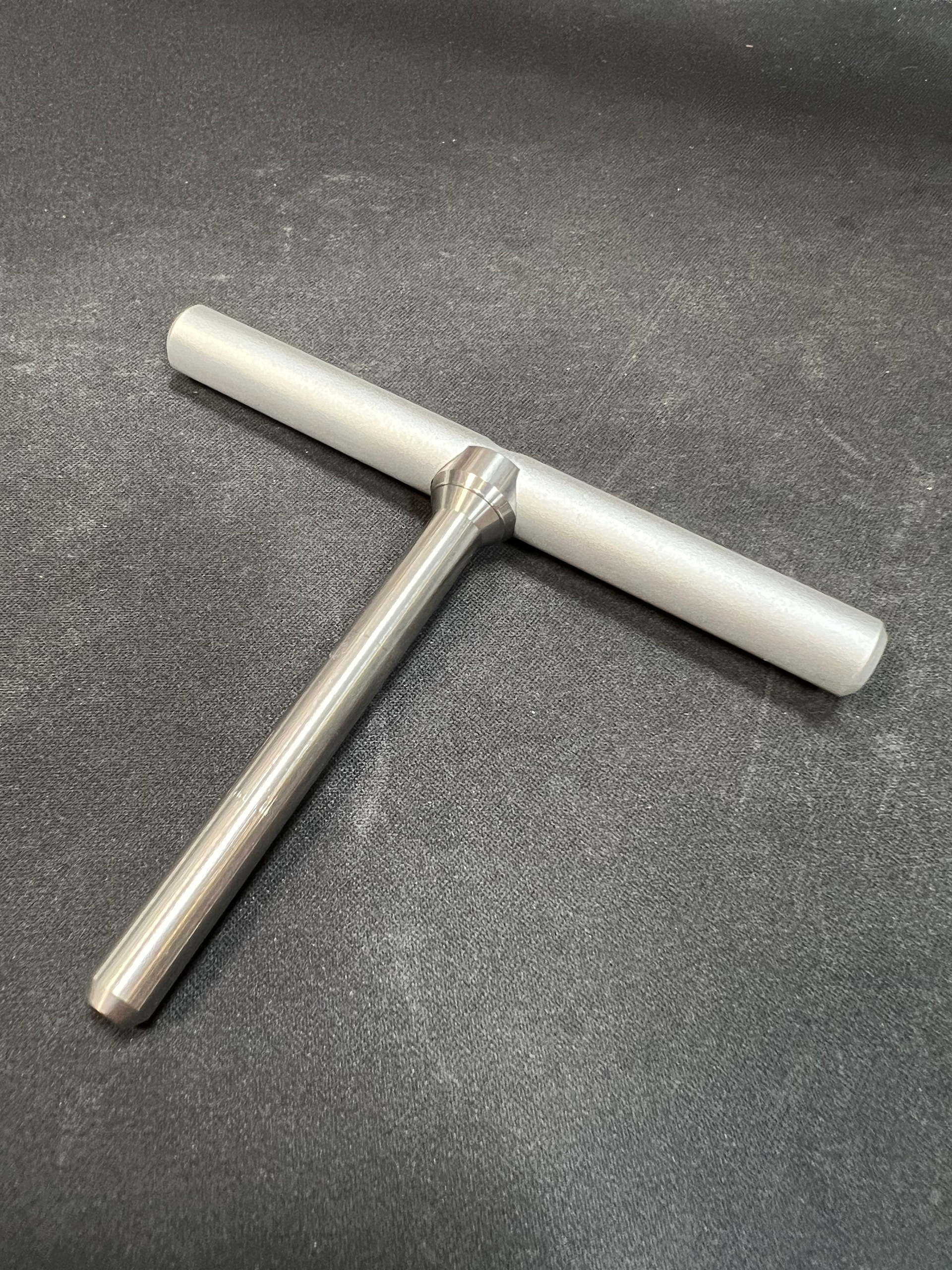
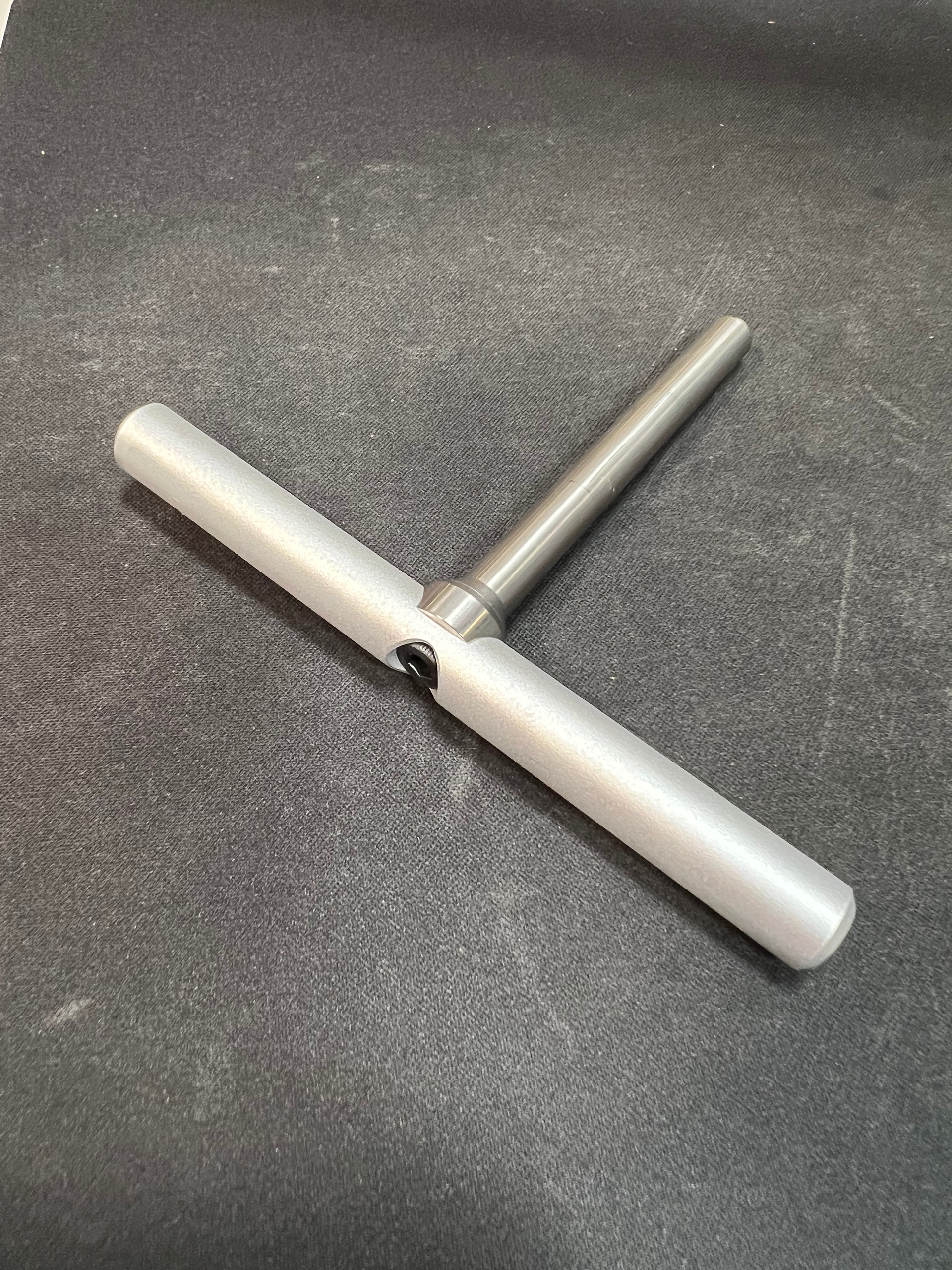
Fully assembled finished tool